Prefabrication & modular construction methods have gained significant traction in construction industry due to their ability to
- Accelerate building processes
- Improve efficiency
- Enhance project outcomes
Building Information Modeling (BIM) plays a vital role in this. It facilitates & optimizes prefabrication & modular construction.
In this article, we will explore how BIM enhances prefabrication and modular construction,
And how it is leading to faster project timelines, improved quality & increased productivity.
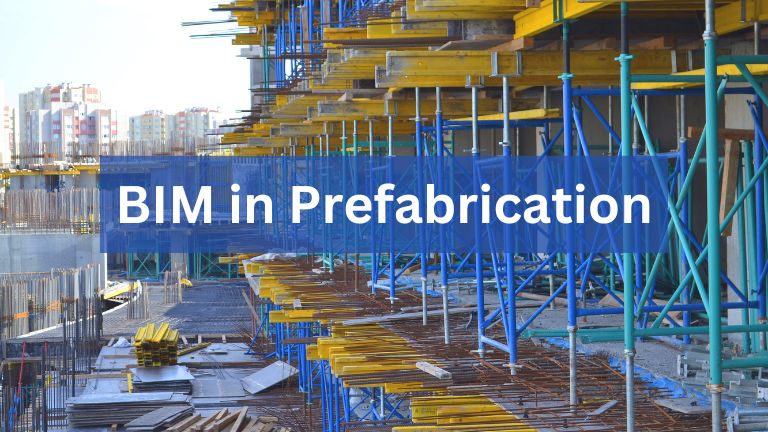
Detailed 3D Modeling
BIM helps with detailed 3D modeling of prefab parts and modular elements.
Designers use BIM to make exact virtual models.
These models are precise, showing the exact size, how things connect, and how they fit with other parts of the building.
It helps see how everything will look and work together before building starts.
BIM can find clashes or issues between different parts of the building, helping to prevent problems later.
With BIM, planners can see potential issues early, which saves time and money during manufacturing and assembly.
BIM ensures that all components fit together seamlessly, enhancing coordination and reducing errors.
Streamlined Design-to-Fabrication Workflow
BIM makes the process from design to building parts smoother.
It connects the design phase with fabrication and assembly stages seamlessly.
Design details from BIM can be directly used by fabricators and manufacturers.
This information is used to generate shop drawings, fabrication details, and production schedules.
This integration stops mistakes and reduces errors.
It ensures smooth transitions and makes processes more efficient.
Improved Collaboration
BIM encourages teamwork among everyone involved in building projects.
Designers, architects, engineers, fabricators & contractors can all work together using BIM.
They collaborate in a shared BIM environment where they see and work on same information in real-time.
This teamwork leads to better design coordination & fewer conflicts during the project.
Collaboration also ensures that all parties own the same goals & are working towards on them together.
Real-time collaboration and information exchange helps improve communication between all team members.
Ultimately, this collaborative approach results in better project outcomes and successful completion.
Clash Detection and Conflict Resolution
BIM helps find clashes or conflicts between different parts of the building.
Clash detection is very important in prefabrication and modular construction.
BIM software can spot clashes between prefabricated components, building systems, and existing structures.
Finding these clashes early helps fix problems before manufacturing and assembly start.
Early clash detection saves money by avoiding costly rework during on-site installation and keeps the assembly process smooth.
Accurate Material Quantification
BIM helps measure materials accurately for prefab parts and modular elements.
Data from the BIM model is used to figure out exactly how much material is needed.
With this data, project teams can create precise quantity take-offs, which help with ordering materials.
Accurate material measurement leads to better supply chain management, saving money and reducing waste.
It makes projects run smoother and more efficiently, leading to better outcomes overall.
Off-Site Construction Planning
BIM helps with planning construction away from the site.
It lets project teams visualize, sequence, and coordinate prefab parts and modular elements.
Teams can use the 3D model to plan
- How parts are put together
- How they’re transported
- How they’re installed.
Planning ahead like this makes construction
- More efficient
- Reduces disruptions on-site
- Keeps the project schedule on track
It’s a proactive way to make sure everything goes smoothly, even before the construction starts.
Enhanced Quality Control
BIM helps ensure high-quality construction in prefab and modular projects.
Project teams can inspect virtually, checking for any issues before things are built.
They can also run simulations to see how things will work in real life.
BIM helps teams validate designs before they’re made, reducing the chance of mistakes.
This ensures that prefab parts meet the needed standards – which results in better-built structures & improved building performance.
Conclusion:
By leveraging the power of BIM in prefabrication and modular construction, projects can achieve accelerated building processes, improved efficiency, and enhanced project outcomes.
The detailed 3D modeling, streamlined workflows, improved collaboration, clash detection, accurate material quantification, off-site construction planning, and enhanced quality control offered by BIM contribute to the success of prefabricated and modular construction projects.